
Opening and closing of the current to coil is then controlled by the minicomputer installed in the engine. A sensor capable of intimating exact position of pistons to engine control unit (ECU) is used instead. Electronic pulses are produced by the pickup coil or the hall effect switch during rotation of distributor, when the reluctor wheel passes by the pickup assembly. Cam lobes are replaced by a trigger wheel, located on the end of the distributor shaft. These timings are so highly significant to an engine performance and health that advanced models of forklift trucks tend to do away with the points.Įlectronic distributors installed in various models of forklift trucks comprise of an electronic coil, a magnetic coil and a hall effect switch. Spark timing is a highly critical action performed in the forklifts. This is done by allowing the breaker points mounting plate to rotate and adjust the spark time associated with high engine revolutions per minute (rpm). These mechanisms serve the purpose of advancing engine timings with respect to the engine load or the engine speed. There may be a vacuum advance or centrifugal advance in action. The point also performs another function of controlling the timing of spark. This function causes the coil to lose its ground, thereby generating a high voltage pulse. The target point is opened whenever the cam pushes the lever. The cam located in the centre of distributor pushes the lever connected to one of the several points. This bottom half section is responsible for breaking the current to the coil, where the ground inside the coil is connected to the breaker points. Previous models of forklift distributors served with breaker points has another section in its bottom half. The rotor spinning past a number of contacts, while the common arrangement is one contact per cylinder, transfers electric pulses to each cylinder during one spin cycle through its spark plugs. During this operation, the pulse is transmitted to the spark plug wire and eventually down to the spark plug placed in the targeted cylinder. While the rotor spins past a number of contact points, keeping one contact per cylinder, a high voltage pulse is produced. The coil connected to the rotor, which spins inside of the distributor cap. The task is performed by the distributor cap and rotor. The foremost job is to distribute high voltage from coil to each of the respective cylinders. The distributor performs several functions. The rotor is present inside the distributor cap, which is located on top of distributor shaft but remains insulated from it and the vehicle’s body. The distributor is comprised of rotating arm, also known as a rotor. It routes high voltage generated by the ignition coil to spark plugs in a precise firing order.
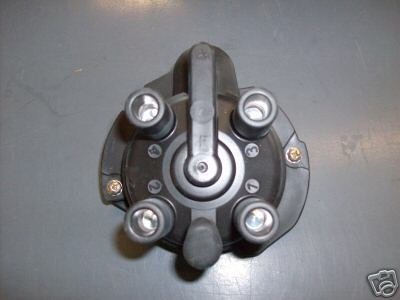
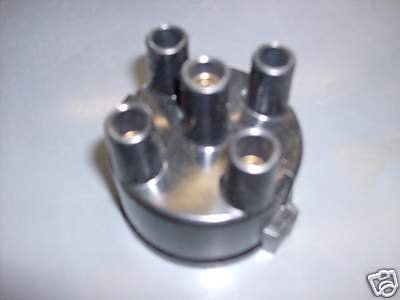
Forklift Distributors are electromechanical devices responsible for delivering or ‘distributing’ spark to the spark plugs at a precise time during ignition cycle of forklift internal combustion engine.
